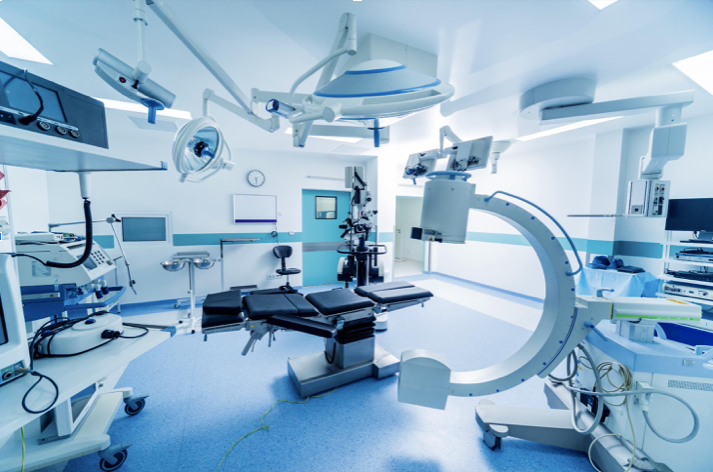
Shell and Tube Heat Exchangers Can Help Avoid Contamination
One of the biggest reasons the shell and tube heat exchangers market is in such a signficant state of growth right now is their use in essential medical devices. As the healthcare industry looks to rise to the challenges of a global pandemic, there’s a need for medical devices made of the highest quality materials. Shell and tube heat exchanges are entrusted in large part due to their ability to fend off contamination through the flow of in-line heating and cooling in medical devices.
The benefits of shell and tube heat exchangers in medical products are numerous. Almost all devices require the cooling or heating of one liquid by another. These two fluids are very rarely the same quality. If these two liquids were to mix, it would contaminate the functionality and safety of the medical device.
Shell and Tube heat exchangers manufactured by Fluorotherm with its proprietary tubing are designed to withstand extreme temperatures and fluids that would corrode in lower-quality tubing. It’s paramount that manufacturers only trust shell and tube heat exchangers from providers who follow strict safety guidelines and protocols. It takes ample testing for shell and tube heat exchangers to receive the clear to be used in medical devices that will help treat the public. There may be differences in quality levels of tubing required based on the corrosive nature of the liquids as well. Every factor must be considered and thought out long before a medical device reaches a hospital.
Different medical devices require different numbers of shells. The number of shells is typically determined by how often fluids need to pass one another in the device. These tubes are often crammed rather close to one another to make the most of the space alotted. As the number of tubes increase, the importance of how they are supported grows. In most instances, many shells will be fastened to a tubesheet within the device. It’s imperative that every spot where the tubes are joined to the tubesheet are thoroughly inspected as this provides another area where leakage can occur. Most devices will utilize a gauge of some sort that will monitor irregularities in pressures, which will provide a clear indication of leakage. Some will simply rely on a double-tubesheet to ensure quality.
Next time you look at a medical device, consider what goes into making that product safe. We take great pride in producing the highest quality shell and tube heat exchangers, so that medical devices can operate to their best ability.