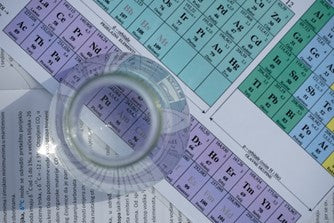
Chemical Processing Essentials: Understanding Proper Tubing Selection
The backbone of the chemical industry lies in its ability to transform raw materials into a vast array of essential products, from fertilizers to the cars we drive. At the heart of this process are fluoropolymer tubing, the unsung heroes that enable modern life as we know it. But not all products are created equal, and selecting the right one is crucial for chemical processing applications.
Why Certain Tubing Reigns Supreme in Chemical Processing
Polymer tubing stands out in the realm of chemical processing for three key reasons:
Chemical Resistance: High-performance tubing boasts unparalleled resistance to a wide range of hazardous substances, from acetone to hydrofluoric acid. Its inert nature makes it a stalwart defender against corrosive, toxic, and flammable chemicals.
Mechanical Properties: With exceptional non-stick and low-friction characteristics, chemical-resistant tubing prevents the buildup of microbes and bacteria, even under high stress conditions. This resilience is vital in maintaining hygiene and efficiency in chemical processing operations.
Thermal Tolerances: Certain types of tubing, such as PTFE, PFA, and FEP, can withstand extreme temperatures ranging from -392°F (-200°C) to 500°F (260°C). This thermal stability ensures consistent performance in challenging environments.
Chemical Processing Needs
The choice of chemical-resistant tubing depends on the specific requirements of the application. Here are some commonly used options:
PTFE (Polytetrafluoroethylene) Tubing: Renowned for its superior temperature and chemical resistance, PTFE is a top choice across various industries. Its non-stick properties and affordability make it a versatile solution for chemical processing.
FEP (Fluorinated Ethylene Propylene) Tubing: Offering excellent chemical inertness and crack resistance, FEP is ideal for applications where flexibility and low stiffness are essential. Its ability to encapsulate components provides added protection in aggressive environments.
ETFE (Ethylene Tetrafluoroethylene Copolymer) Tubing: Known for its exceptional abrasion and impact resistance, ETFE is preferred for housing wiring harnesses and in applications where durability is paramount.
PVDF (Polyvinylidene Fluoride) Tubing: Recognized for its hardness and toughness, PVDF is akin to steel in its resilience. Its resistance to corrosive substances and heavy loads makes it indispensable in chemical manufacturing.
Choosing the Right Product
When it comes to choosing the right high-performance tubing for chemical processing applications, several crucial factors come into play. One of the foremost considerations is chemical compatibility. Different types of products have varying levels of resistance to specific chemicals, acids, and solvents commonly encountered in chemical processing environments. Therefore, it's essential for industry professionals to thoroughly assess the chemical composition of the substances they will be handling and select tubing materials that are chemically compatible to prevent degradation or contamination.
Additionally, the temperature range within which the tubing will operate is a critical factor to consider. Fluorinated products offer exceptional thermal stability, but the temperature resistance varies depending on the specific material composition. For instance, PTFE tubing can withstand extreme temperatures ranging from -392°F (-200°C) to 500°F (260°C), making it suitable for high-temperature applications. Understanding the temperature requirements of the chemical processing operation is vital for selecting the right materials that can maintain their integrity and performance under the intended operating conditions.
Mechanical properties such as flexibility, durability, and tensile strength also play a significant role in determining the suitability of the tubing for chemical processing. The product must be able to withstand the mechanical stresses, pressure fluctuations, and abrasive conditions commonly encountered in industrial environments without compromising performance or structural integrity. By carefully evaluating the mechanical properties, industry professionals can choose materials that offer optimal durability and longevity in their specific applications.
Conclusion
In summary, selecting high-performance tubing for chemical processing requires a comprehensive understanding of factors such as chemical compatibility, temperature resistance, and mechanical properties. By considering these critical factors and choosing the appropriate materials, industry professionals can ensure reliable performance, chemical resistance, and longevity in their operations, ultimately enhancing productivity and safety in chemical processing environments.