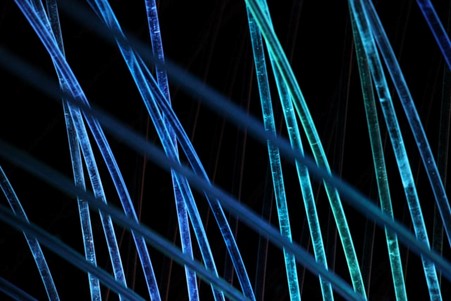
Heat Shrink Tubing - An Industrial Staple
Also referred to as electrical shrink tubing, heat shrink tubing is a typical and vital component in most electrical setups.
Heat shrink tubing is important for any electrical array because it protects electronic systems from damaged cables and electrical components caused by external contaminants. These include sharp objects, moisture, abrasion, and dust. These damages will eventually lead to shorts and failures within electrical circuits.
It also connects loose connectors, joints, wires, splices, and terminals, resulting in better structured and manageable bundles. Heat shrink tubing is important for any modern facility or home. Let's go over what it is exactly, the materials used to make it, and the benefits of its use.
The Product Explained
Heat shrink tubing is a thermoplastic tube that, when heated, shrinks radially to suit the curves of electrical components and wires, forming a protective covering against the elements. Heat shrink tubes may protect against cuts, moisture, and dust by protecting single wires or swarming over almost the entirety of electrical setups.
Plastic makers will often extrude a standard thermoplastic tube to kickstart the process of the creation of heat shrink tubing. After the required plastic has been extruded, it is heated and forced to expand, increasing the diameter of the tube. Afterward, the inflated tubing is allowed to cool to room temperature before its utilization.
The inflated thermoplastic tube is then heated to a specific temperature and wrapped around the wires or other required components, thus forming the aforementioned protective layer of plastic.
Materials
In comparison to its tape wiring and dip coating counterparts, heat shrink tubing can often be sold with specific additives to enhance its performance and is made from a wide range of thermoplastic materials. Nonetheless, these are three of the most common materials used for heat shrink tubing:
- Polyolefin: Because of its heat resilience, polyolefin is the most often used material for shrink tubing, with the material can withstand extreme temperatures of up to 125 °C to 135 °C. Polyolefin is an excellent solution for industrial companies operating in heat-trodden environments.
- PVC: A cheaper alternative to polyolefin, PVC is incredibly resistant to abrasion and notorious for its durability and strength. Nonetheless, its lower price tag is reflected in its downgraded ability to withstand high temperatures, with its highest resistance threshold being 105 °C.
- Adhesive-Lined Polyolefin: Manufacturers have also designed a polyolefin heat shrink tubing enhanced with a key additive in the form of adhesive-lined polyolefin. The material is made with a sticky inner layer that melts and binds to the wires and components within the tube to provide a snug fit to ensure it will not slip in important situations.
Pros of Using Heat Shrink Tubing
- Protection against moisture, sharp-cutting edges, chemicals, dust, and other contaminants.
- Finished and smooth appearance.
- Easy organization of cables and wires via color coding systems.
- Thermal and electrical insulation properties.
- Better structural support causes less stress on wires and components.
Wrap Up
Heat shrink tubing has an endless list of applications mainly used in the electronics, automotive, transportation, and telecommunications industries. Whether looking to provide some protection for a home or company's electrical system against the elements, this material is an incredibly wise choice – especially the case in scorching environments.