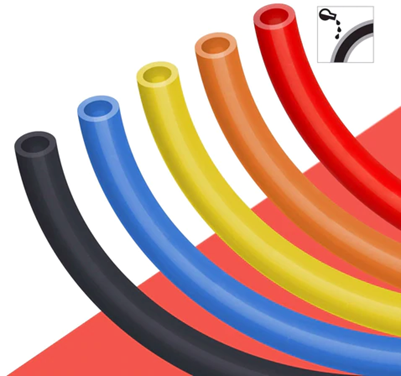
Seven Most Common Fluoropolymer Coatings
Interested to know which are the most common fluoropolymer coatings used in manufacturing? Here’s a quick summary, and read on for more details about the ways they are applied:
- PTFE (Polytetrafluoroethylene)
- FEP (Fluorinated Ethylene Propylene)
- PPS (Polyphenylene Sulfide)
- PVDF (Polyvinylidene Fluoride)
- TFE (Tetrafluoroethylene)
- FEVE (Fluoroethylene Vinyl Ether)
- ETFE (Ethylene Tetrafluoroethylene Copolymer)
They're used to strengthen industrial and commercial parts found in vital equipment. But choosing the perfect one can be tricky. So, learn more about each type below.
PTFE (Polytetrafluoroethylene)
PTFE coatings are often applied to food-centric utensils and equipment to ensure it meets FDA standards. It boasts non-stick and easy-cleaning properties, making it perfect for bakeware.
Once applied to the product, the PTFE-coated sections can withstand temperatures as low as -100 degrees Fahrenheit and as high as 400 degrees Fahrenheit.
FEP (Fluorinated Ethylene Propylene)
Like PTFE, FEP coatings are primarily utilized in the food and beverage industry. Industrial settings particularly benefit from it, thanks to its resistance against electrical, mechanical, and chemical variables.
With that said, it's also the go-to for:
- Semiconductor wet bench equipment
- Pump housings
- Pipe linings
- Fluid handling equipment
- Chemical processing equipment
- Medical components
Essentially, anything needing low stiffness, crack resistance, and chemical inertness can benefit from the fluorinated ethylene propylene coating.
PPS (Polyphenylene Sulfide)
PPS is seen in various industrial applications. It's widely respected for enhancing chemical manufacturing parts. However, it's also popular in the food and beverage industry, automotive sector, and medical laboratories.
Due to its chemical- and wear-resistance, polyphenylene sulfide works wonders to strengthen parts utilized in high-pressure environments.
A study conducted on the usage of PPS in America concluded the demand for the coating within the automotive industry stems from its use in:
- carburetor parts
- flow control valves found in heating systems
- exhaust gas return valves
- ignition plates
Parts treated with the coating can withstand ultra-high temperatures between 425 and 700 degrees Fahrenheit.
PVDF (Polyvinylidene Fluoride)
Typically found in chemical manufacturing, refineries, oil and gas, and similar industrial sectors, PVDF is as hard as steel. It's often applied in thick slathers to deal with adverse conditions, heavy loads, and corrosive substances.
Coated parts benefit from increased longevity and unmatched toughness against wear and tear from prolonged use.
TFE (Tetrafluoroethylene)
The aerospace, automotive, and manufacturing industries often utilize TFE. It's applied to spline shafts, screws, and other functional parts to:
- guarantee the balance of airplane parts like propellers
- reduce friction and stress on machine parts
- improve the torque of specific vehicle components
FEVE (Fluoroethylene Vinyl Ether)
FEVE coatings are used in both industrial and architectural sectors. It boasts excellent corrosion resistance and protects against wind, dirt, chemicals, UV rays, and precipitation.
The coating technology helps retain color and gloss for over 30 years, ultimately reducing the lifecycle coating costs.
ETFE (Ethylene Tetrafluoroethylene Copolymer)
ETFE is popular in the roofing industry. It's solid yet flexible and offers unbeatable UV resistance.
Additionally, it's found in:
- Cryogenics
- Gaskets
- Bearings
- Pharmaceutical film packaging
- Process vessels
- Wire insulation
- Electrical components
The Bottom Line
Every fluoropolymer coating type has its own uses, strengths, and weaknesses, giving each a special place in all applications.