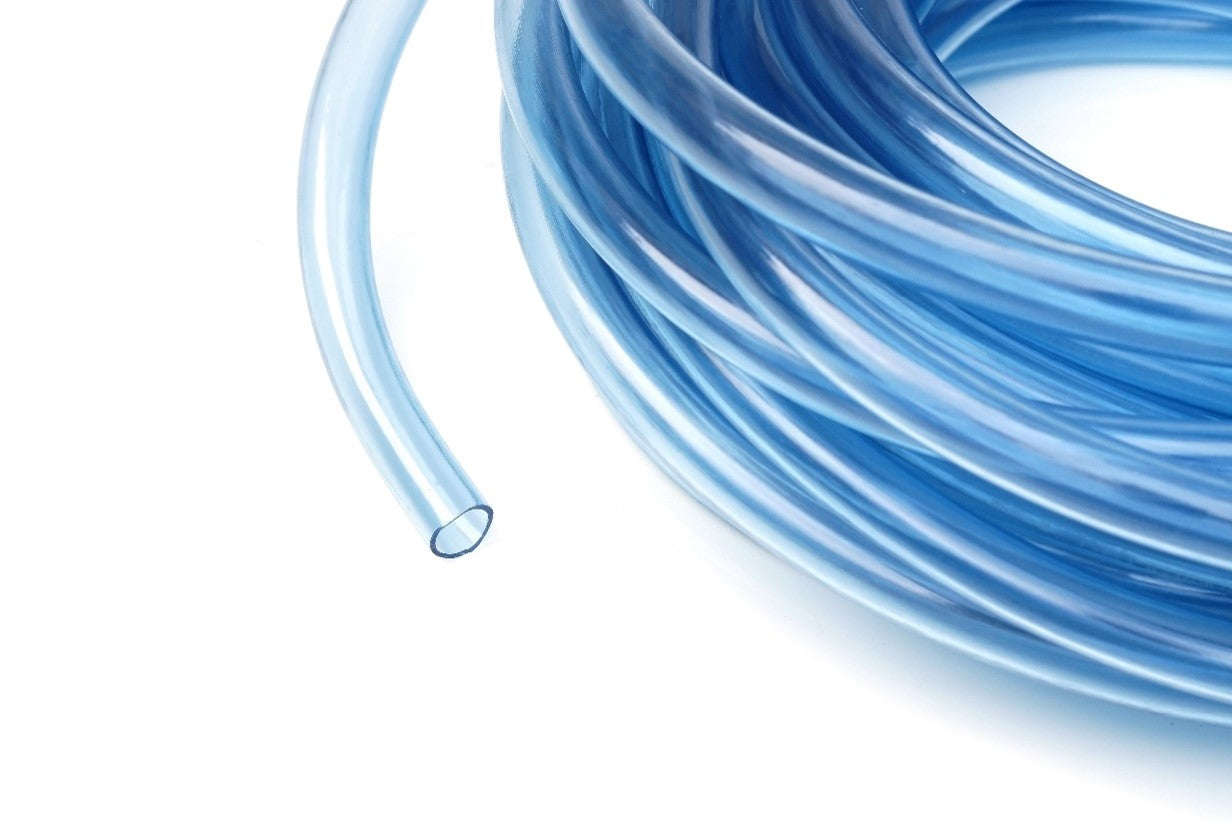
Why Fluoropolymers Outperform Leading Materials
In the world of tubing materials, the choice between various types can be overwhelming, especially when functionality and efficiency are at stake. Among these, PTFE (Polytetrafluoroethylene) tubing stands out above the rest for its unique properties. But how does it compare to other popular tubing materials like PVC, stainless steel, and rubber? This blog delves into a comparative analysis of these materials, evaluating them across various parameters such as durability, chemical resistance, flexibility, and applications.
Understanding PTFE Tubing
PTFE, commonly known by the brand name Teflon, is renowned for its remarkable resistance to high temperatures, chemicals, and its non-stick properties. It operates efficiently in temperatures ranging from -454°F to 500°F, which is an exceptionally significant range compared to other materials. Its inertness to most chemicals makes it ideal for handling corrosive substances. Moreover, its low coefficient of friction and non-reactive nature makes it a preferred choice in many industrial, chemical, and medical applications.
PTFE vs. PVC Tubing
PVC (Polyvinyl Chloride) tubing is another popular choice, known for its versatility and cost-effectiveness. However, when compared to PTFE, PVC falls short in several areas. PVC can typically withstand temperatures only up to 140°F, making it unsuitable for high-temperature applications. Additionally, PVC can start to degrade when exposed to harsh chemicals, unlike PTFE. However, PVC is more flexible than PTFE, which can ultimately be the deciding factor in specific applications where flexibility is crucial.
PTFE vs. Stainless Steel Tubing
Stainless steel tubing is often chosen for its strength and resistance to rust and corrosion. It can also handle high-pressure applications better than PTFE. However, PTFE outshines stainless steel in chemical resistance and is much lighter, making it easier to handle and install. Furthermore, PTFE's non-stick surface ensures that materials flow smoothly through the tubing, a property that stainless steel cannot match.
PTFE vs. Rubber Tubing
Rubber tubing is favored in applications requiring high flexibility and elasticity. However, PTFE beats rubber when it comes to temperature and chemical resistance. Rubber tubing can degrade under extreme temperatures and exposure to certain chemicals, whereas PTFE maintains its integrity. However, in applications requiring a high degree of flexibility and bendability, rubber may be the preferred choice.
Applications
- PTFE Tubing is predominantly used in high-temperature environments, chemical processing, and in the medical industry for catheters and fluid transfer systems.
- PVC Tubing is suited for general low-pressure industrial applications, for transporting liquids, gases, and some chemicals.
- Stainless Steel Tubing is ideal for high-pressure applications, in the oil and gas industry, and in hydraulic systems.
- Rubber Tubing is commonly used in medical devices, laboratories, and pneumatic systems, where flexibility is essential.
In conclusion, while each material has its own set of advantages, PTFE tubing stands out for its exceptional chemical and temperature resistance, as well as its non-stick properties. However, the final choice should always be governed by the specific requirements of each application, considering factors like temperature range, chemical exposure, flexibility needs, and pressure requirements. Understanding the unique properties and limitations of each material ensures the selection of the most appropriate tubing for any given application.